Pracuję z przemysłem od 2001 roku i wiem, że największy potencjał do jego rozwoju leży u dołu piramidy. Pielęgnowany w odpowiednich warunkach sprawia, że przeciętne zespoły osiągają dla swoich firm nieprzeciętne wyniki.
Marcin Szymański
W mojej pracy z zespołami łączę:
- twarde techniki optymalizacji: lean i problem solving
- miękkie narzędzia psychologii i wpływu społecznego
- ze zwinnością projektów (agility) i odpornością zespołów (resilience).
W ten sposób, tylko w latach 2016-18 współpracowałem z 220 zespołami ds. optymalizacji z 64 fabryk z legnickiej, wałbrzyskiej i pomorskiej SSE.
Pod moją opieką zespoły te wykonały kilkaset diagnoz, w których zidentyfikowały ponad 730 czynników o negatywnym wpływie na procesy w ich firmach. Dzięki temu zainicjowaliśmy ponad 650 projektów optymalizacyjnych – wdrożeń, w które zaangażowało się ponad 1600 menedżerów, inżynierów, techników i operatorów maszyn.
Dostarczyli oni oszczędności swoim firmom na poziomie 86,7 mln złotych. Każdy z zespołów w trakcie realizacji zadań po warsztatowych przeciętnie generował wartość dodaną dla swojej firmy lub usprawnienie w przeciętnej wysokości 190.000 PLN.
Metody pracy
Na poziomie strategicznym, na którym wyznaczam cele – korzystam z narzędzi: Total Quality Management, Hoshin Kanri i Balanced ScoreCard.
Na poziomie operacyjnym, gdzie uruchamiam projekty optymalizacyjne – stosuję metody tj.: 8D, A3, RCA, FMEA, Agile, SIPOC, SCRUM, TPM, SMED, KAIZEN, 5S itp. Uczę identyfikować MUDĘ, kontrolować koszty i utrzymywać długotrwałe efekty zmian. W pracy konsultanta wykorzystuję metody visual management, mind mapping, jak również tradycyjne metody zarządzania projektami tj.: harmonogramy Gantta i CPM.
Wpływam na motywację zespołów. Rozwijam w nich autonomię i poczucie wspólnych celów. Wzmacniam ich Geny odporności®. Zmieniam ich sposób działania i myślenia, dlatego szybko stają się lepsze i wydajniejsze niż kiedykolwiek wcześniej.
Co roku prowadzę średnio 150 dni szkoleniowych i konsultacji. Do tej pory przeprowadziłem około 10.000 godzin warsztatów i kilka tysięcy godzin projektów wdrożeniowych.
Całościowe spojrzenie i unikalne kompetencje pozwalają mi skutecznie prowadzić projekty dla najbardziej wymagających firm i wpływowych korporacji.
Współpracowałem z interdyscyplinarnymi zespołami z wszystkich szczebli organizacji: menedżerów, inżynierów, specjalistów i pracowników operacyjnych, z działów produkcji, UR, R&D, jakości z takich branż:
- automotive: AKS, Antolin Grupo, Borgers, Daicel Safety System Europe, Eldisy, Faist Chem, EPP, Faurecia, Gates, Haerter, Hendrickson Automotive, HMT, JOST, JoysonQuin, Korean Al Casting, Lear Corporation, MANDO Corporation, Mercedes Benz Manufacturing Poland, Nordglass, NSK, Yagi Poland Factory, Jelcz PGZ, JoysonQuin Automotive Systems Polska, Polmo SA, Polimer, Ronal Group, Sanden Manufacturing, Sohbi Craft Poland, Toyota Boshoku, TMR Plastics, Tristone Flowtech, Vissher Caravelle, VICIM, Winkelmann automotive,
- elektrotechniczna: Camsat, Emtor, EPP, Lenze, PTOM, Renex, Sharp Manufacturing, Tecsolum, TeleFonika, Teleplan, Viessmann, Unimetal, Winkelmann Group, Xylem,
- metalowa: Bagramet, Grupa Seppeler, Expom SA, Kołaszewski, nVENT, Opakmet, PESA SA, Privacon, Stiegelmeyer, ZNTK Paterek,
- chemiczna: HELM AG, Lifocolor, Purinova, PCC Rokita, Thermaflex,
- handlowa: Auchan Polska,
- meblarska / wyposażenia wnętrz: Adeo Sreens, Anwis, Bydgoskie Meble, C+P Systemy meblowe, Gabi Bis, Gala Collezione, Etap Sofa, Franc Gardiner, Helvetia Furniture, IMS Sofa, Karolina Zakłady Porcelany, Muller Świece, Rejs, Schoeneberger, Sieper, Sklejka Multi, ZORKA Meble, ZEBRA,
- opakowania: Can-pack, Empac, Haber, Hanplast, Iris, Neupack, OKT, Opakofarb, Pasaco-Dominex, Rotom, Walsroder,
- medyczna / farmacja: Bausch Health, TZMO Plastica,
- rolno – spożywcza: Abramczyk, ADM, Agrifirm, Agriplus, Bista Standard, Bungee, Chemirol, Dalgety, De Heus, Dr. Oetker, Drobex, Frosta, Frigo Logistic, Greenyard, Grupa Graal, Gzella, Indykpol, Jagr, Jaskot, Kapitan NAVI, Konspol, Krajowa Spółka Cukrowa, Kopernik SA, Louis Dreyfus, MARWIT, Narolco, Probio, Osadkowski SA, Osadkowski-Cebulski, Sokołów SA, Stock Polska, ZM Skiba, ZPC Otmuchów, i in.
Jakie metody szkoleniowe stosuję?
Learning by doing
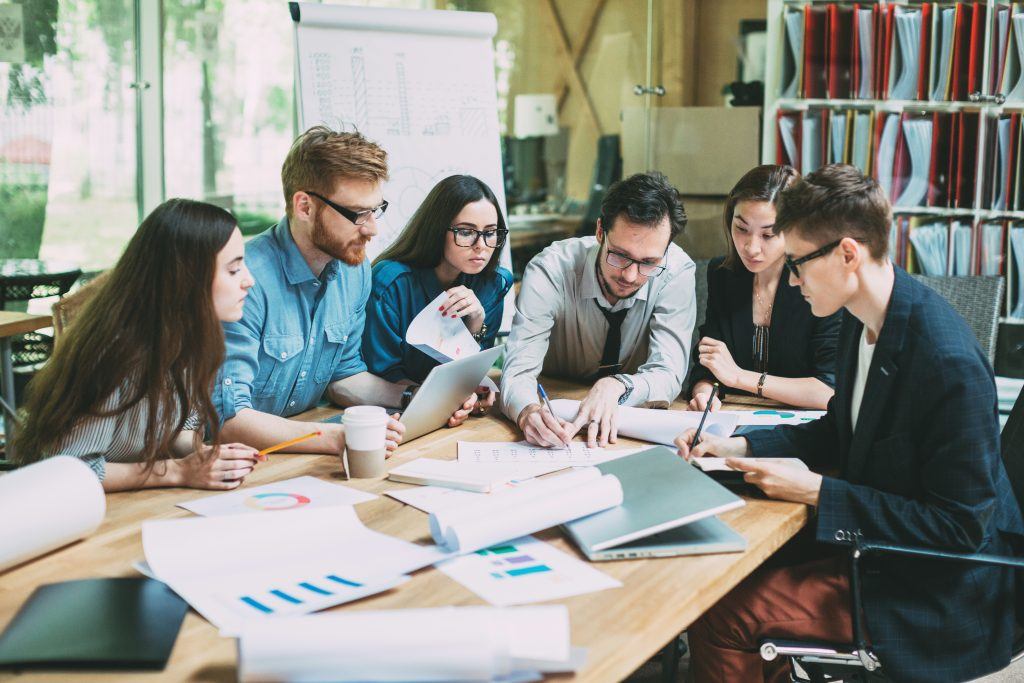
Uczymy się przez działanie. To najskuteczniejszy sposób w procesie rozwijania kompetencji u osób dorosłych.
Sam pracowałem w przemyśle jako kierownik produkcji przez 4 lata, a od 15 prowadzę projekty szkoleniowe i doradcze. W praktyce szkoleniowej pracuję z grupami tak samo efektywnie w salkach konferencyjnych jak i na stanowiskach pracy i w procesach na halach produkcyjnych. Wykorzystuję cykl Kolba i przeprowadzam zespoły przez jego 4 fazy: fazę doświadczeń, sesję refleksji, sesję ugruntowania teoretycznego zdobytej wiedzy i sesję jej zastosowania w praktyce.
Pracuję na trójkącie kompetencji – wzmacniając wśród moich uczestników jednocześnie obszar wiedzy, umiejętności i postaw. W ten sposób staram się mieć wpływ dostarczenie oczekiwanych przez moich klientów twardych efektów naszej pracy. Dzięki usystematyzowaniu nabytej w praktyce wiedzy na kursach trenerskich korzystam z trzydziestu metod szkoleniowych. Są to:
- prezentacje
- wykłady
- gry
- filmy
- ćwiczenia
- praca w grupach
- praca indywidualna
- dzielenie się rolami
- odgrywanie scenek
- dyskusje
- ice-breakery
- energizery
- inhibitory
- testy
- praca z tekstem lub nagraniem
- burze mózgów
- in basket
- kapelusze De Bono
- case studies
- case stories
- symulacje
- story-telling
- instruktaże
- demonstracje
- quizy
- debaty oksfordzkie
- sesje pytań i odpowiedzi
- sesje world cafe
- metodę kuli śniegowej
- metodę akwarium
Dla kogo prowadzę szkolenia?
W latach 2016-18, spośród ponad 1600 osób uczestniczących w szkoleniach z zakresu lean management i problem solving, 58% tworzyło zespoły multidyscyplinarne, 34% zespoły produkcyjne, 5% zespoły KJ, a tylko 3% z działu logistyki.
Mniej więcej na 3 mężczyzn przypadała jedna kobieta, 48% uczestników okazywało się wyższym, 40% średnim, a 12% zawodowym wykształceniem. 32% uczestników moich szkoleń były to osoby w grupie wiekowej 24-35 lat, 44% – 36-45 lat, 18% – 46-55 lat. Niestety tylko 6% uczestników były to osoby najbardziej doświadczone z grupy 55+.
Nie ma znaczenia czy uczestnik mojego szkolenia był inżynierem, prezesem zarządu, operatorem maszyny, czy kontrolerem jakości. Nie ma znaczenia, czy ukończył elitarny kurs MBA czy ma wykształcenie zawodowe – KAŻDY był dla mnie tak samo ważny.
Ponieważ KAŻDY mógł mieć wpływ na rezultaty projektu, niezależnie czy znajdowaliśmy się właśnie w fazie planowania, transformacji, czy utrzymania trwałości wyników – z wielką pokorą podchodziłem do specyfiki stanowiskowej i doświadczeń moich słuchaczy, dlatego każdy uczestnik moich szkoleń miał prawo czuć się dla mnie WAŻNY.
Jakie są opinie o mojej pracy?
Co o mnie piszą?
”Niebanalne podejście – nigdy nie widziałem takiej interpretacji powszechnie znanego standardu” – Opinia doświadczonego inżyniera jakości, uczestnika warsztatów 8D.
Do wyspecjalizowanych szkoleń inżynierskich lean manufacturing i problem solving z sukcesem wprowadzam elementy rozwoju interpersonalnego, tj.: znane ze szkoleń menedżerskich mechanizmy wpływu społecznego, zasady kierowania i komunikacji, delegowania i rozwoju oraz budowania zespołów. Dzięki temu moje warsztaty oceniane są jako wnoszące świeże spojrzenie nawet na doskonale znane mechanizmy.
Swoimi doświadczeniami na temat łączenia wiedzy technicznej z umiejętnościami interpersonalnymi dzielę się w książce pt.: “Przekonaj pracowników do dbania o jakość” [wydawnictwo Difin, Warszawa 2010].
Na zakończenie każdego szkolenia zawsze proszę grupę, aby podzieliła się ze mną refleksjami z moich warsztatów.
Oto niektóre z nich:
“Profesjonalne podejście do szkolenia, super metody tłumaczenia”;
“Kompetencje i prosty przekaz wiadomości”;
“Super szkolenie, doskonałe tłumaczenie zagadnień”;
“Otwartość na zespół, konstruktywna krytyka, dobra komunikacja”;
“Pozytywne nastawienie, uśmiech i zaangażowanie”;
“Dużo zagadnień praktycznych i pracy w grupach”;
“Mam inne – lepsze spojrzenie na temat szkolenia. Bardziej pozytywnie odbieram teraz procesy i uważam, że też tak będą odbierane przez innych”‘
“Rzeczowe, merytoryczne podejście, w przystępny sposób, poparte praktyką i przykładami”.
Wiem, że niełatwo jest współpracować z zespołami złożonymi ze specjalistów i inżynierów, z brygadzistów i mistrzów, z szefami komórek i pionów, z dyrekcją zakładów i przedstawicielami zarządów, z operatorami maszyn i pracownikami produkcji. Dlatego do każdej z grup podchodzę elastycznie i dostosowuję sposób przekazu i przykłady, płynnie przeplatając wiedzę specjalistyczną i menedżerską z inspirującymi historiami z własnej praktyki. Słucham swoich rozmówców i notuję, co jest dla nich ważne.
Oto kilka deklaracji uczestników co chcą zmienić w swojej pracy po zakończeniu szkolenia.
“Przyspieszyć procesy, eliminować MUDA”;
“Skupić się nad błędami, które popełniam w firmie i wyeliminować je raz na zawsze”;
“Zmienić swoje postępowanie wobec zespołu i usprawnić cały dział”;
“Zastosować metody problem solving nietuzinkowo – znajdować im lepsze, bardziej efektywne zastosowania”;
“Zmienić standardowe podejście do znanych nam narzędzi Lean i Problem solving – korzystać z nich lepiej i efektywniej niż stosujemy je dziś”;
“Wziąć przykład z sukcesów i porażek innych firm – przedstawianych przez trenera”;
“Zmienić na skuteczniejszy schemat rozwiązywania problemów produkcyjnych firmy”;
“Poprawić relacje ze współpracownikami ale doskonalenie zacząć od siebie…”
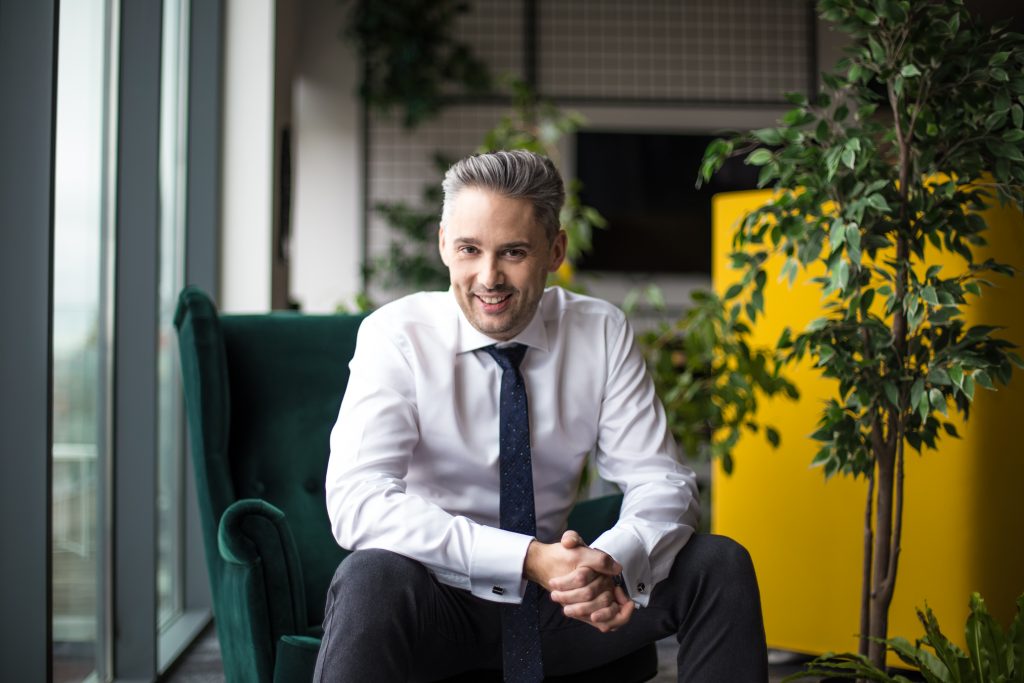